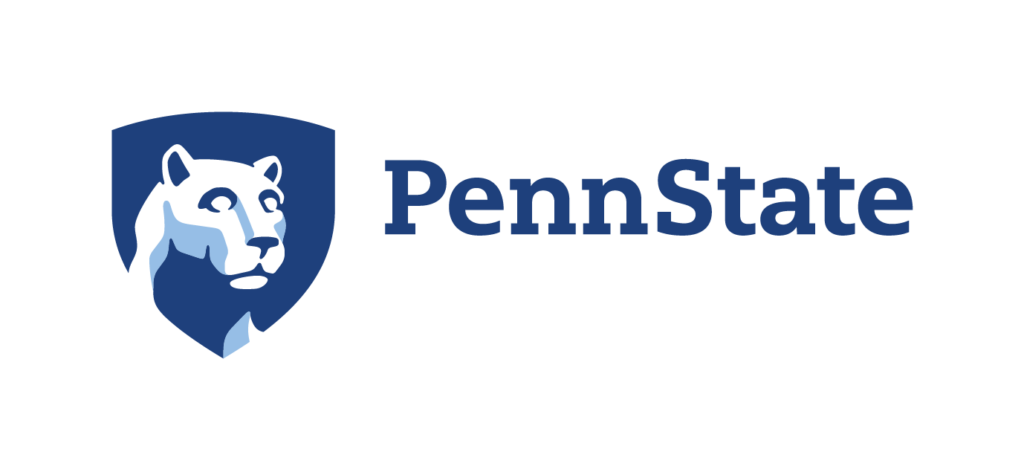
EXTRUDE HONE PARTNERS ON A PROJECT WITH PENNSYLVANIA STATE UNIVERSITY
Thanks to his founder’s spirit, Extrude Hone has always been at the forefront of innovation.
Today, Extrude Hone is an Industry Partner who supports one of the projects from Pennsylvania State University within its Manufacturing PA Innovation Program. This project involves Process development and physics modeling of orbital flow machining.
Who is Penn State, and what is the Manufacturing PA Innovation Program?
Consider Penn State’s Mission and Values:
“The Pennsylvania State University is a multi-campus, land-grant, public research university that educates students worldwide and supports individuals and communities through integrated teaching, research, and service programs. “
Penn State was founded in 1855 with an original focus on agriculture. Since then, it has expanded the scope of its activities to land, space, the sun, and even the sea.
It is at the cutting edge of research, with a record-breaking $1.2B annual research expenditure. Its 24 campuses across Pennsylvania ranks in the top 6% of world-class universities. It welcomes about 88,000 students from 50 states and 140+ countries.
Focusing on research, they cover twelve disciplines, including material engineering, and this is where we meet.
On April 5th, the Manufacturing PA Innovation Program runs the sixth annual Manufacturing PA Innovation Program Expo at the Commonwealth Keystone Building in Harrisburg, PA.
This is a fantastic opportunity to highlight the partnerships between faculty, students, and manufacturers to develop new processes and enhance products and technologies.
The expo is a great networking opportunity to learn more about the manufacturer’s products, services, and more.
Extrude Hone Orbital AFM the process in detail.
Extrude Hone invented and patented the Abrasive Flow Machining (AFM), also called Extrude Honing. AFM encompassed several variations: the traditional two-way flow, the one-way flow iteration, the MICROFLOW-specific flow tuning version, and the Orbital AFM.
We will focus on that latest.
Orbital AFM has been specifically engineered to address mold polishing, which requires a surface requirement of 0.05µm or below. Manufacturing them is labor-intensive and costly.
Orbital Abrasive Flow Machining (OAFM) by Extrude Hone
The orbital Abrasive Flow Machining (OAFM) process came to fruition within the ORBITEX machine.
In Orbital AFM, surface and edge finishing is achieved by rapid, low-amplitude oscillations of the workpiece relative to a self-forming elastic plastic” abrasive polishing tool.” The “tool” is a “pad” or layer of abrasive-laden elastic-plastic media, like that used in extrusion abrasive flow finishing but typically higher viscosity and more elastic.
The general concept is to provide a translational motion of the workpiece as a portion of its geometry encounters, compressively displaces and tangentially “slides” across a complementary portion of the compressed elastic plastic self-formed “pad” (comprised of a layer of Extrude Hone’s particular viscous-elastic abrasive media) positioned on the surface of a “displacer”- that is roughly a mirror image of the workpiece, plus or minus a “gap”- accommodating the layer of media and a clearance.
A small (0.5 to 5 mm) circular eccentric oscillation is applied to the workpiece so that, at any point in its oscillation, a portion of its surface “bumps” into the media “pad,” elastically compresses it (5 – 20%) and slides across as it moves along its orbital oscillation path.
As the circular eccentric oscillation continues, the portions of the workpiece sliding across the media “pad” progress around the entire geometry of the workpiece with the eccentric path.
Ultimately, the whole circular oscillation will have engaged each portion of the surface.
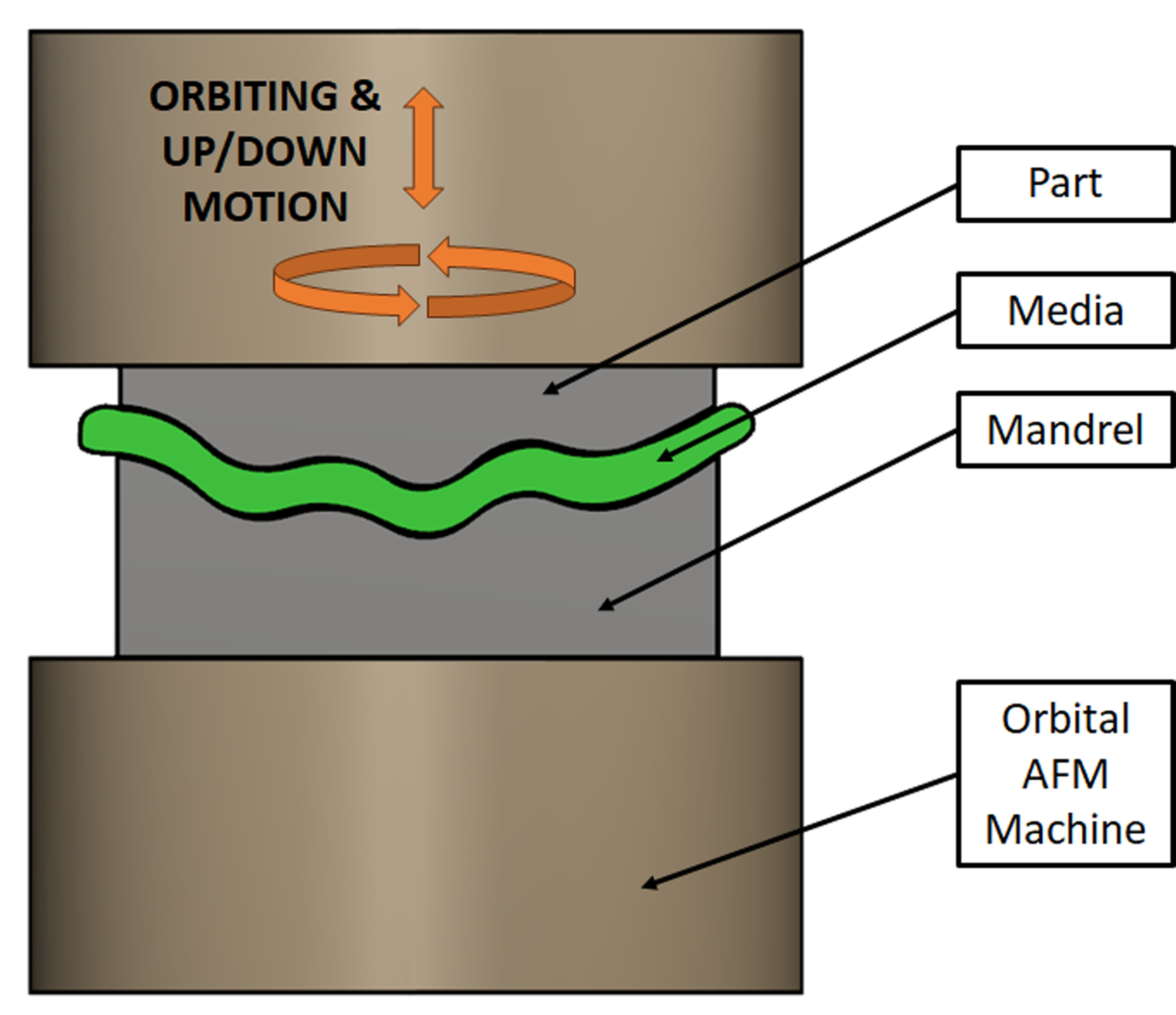
The plane of oscillation can change during processing to treat all surfaces equally for complex three-dimensional geometries. Otherwise, surfaces parallel to the rotation plane will always (or never) be in contact with the abrasive media “pad.”
Orbital AFM benefits
Using equipment that oscillates both vertically and orbitally offers a universal strategy to deal with surfaces of almost any geometry.
With a simultaneous linear oscillation along an axis perpendicular to the circular oscillation, ideally of equal amplitude and nearly, but not quite, the same frequency as the circular oscillation, the resultant path is an elliptical oscillation plane that “nutates” or whose oscillation plane slowly “wobbles.” Consequently, every surface is, on average, “bumped” against equally.
To assure uniformity, the highly elastic abrasive media must be somewhat plastic to be “self-forming” and continually present “fresh” media to the polishing gap.
For finishing most applications, Extrude Hone’s special AFM media materials allow using simple arrangements for feeding and evacuating the abrasive media “pad” to achieve uniform results :
- Regions of the media “pad” that over-fill the gap generally get pushed aside and are shaped by the oscillation of the workpiece itself.
- Regions of media in the gap that are worked excessively become warmer due to deformation heating and consequently become less elastic and more plastic and are squeezed out of the work gap.
Orbital AFM’s small (0.5 – 5 mm) oscillation amplitude allows for finishing highly complex geometries since all areas except internal features that are more minor than the oscillation amplitude work equally in the process :
- The controlled and cushioned, but still repeated, “bumping” of the workpiece against the self-shaped tool imparts beneficial residual compressive stresses to the workpiece surfaces.
- The tangential translation of the workpiece across the elastically compressed and “cushioned” abrasive particles provides remarkable improvements in surface roughness.
The Penn State take at Orbital AFM
Unfortunately, the process is still imperfect and could fall short with some applications due to more stringent requirements. It becomes challenging to use this technology to process some high-performance components uniformly.
Extrude Hone wishes to solve this problem by partnering with the Manufacturing PA Innovation Program. The institute would bring engineering science and analytical tools to tackle that challenge.
This is how the collaboration took shape in 2023 and is currently developing.
The “Process Development and Physics Modeling of Orbital Abrasive Flow Machining” Project
The objectives of the proposed work are to
- establish an engineering science base and simulation analysis framework to enable Extrude Hone engineers to apply their existing technology better.
- explore novel methods to advance OAFM technology significantly.
Ph.D. Student Hakan Toykoc (picture) carries out this work under the supervision of Professors Edward De Meter and Saurabh Basu.
The project is called “Process Development and Physics Modeling of Orbital Abrasive Flow Machining.”
A grant from the Commonwealth of Pennsylvania Department of Community & Economic Development finances this project.
At the core of their proposed solution are detailed OAFM processing experiments to understand the various parameters involved and establish their relationships.
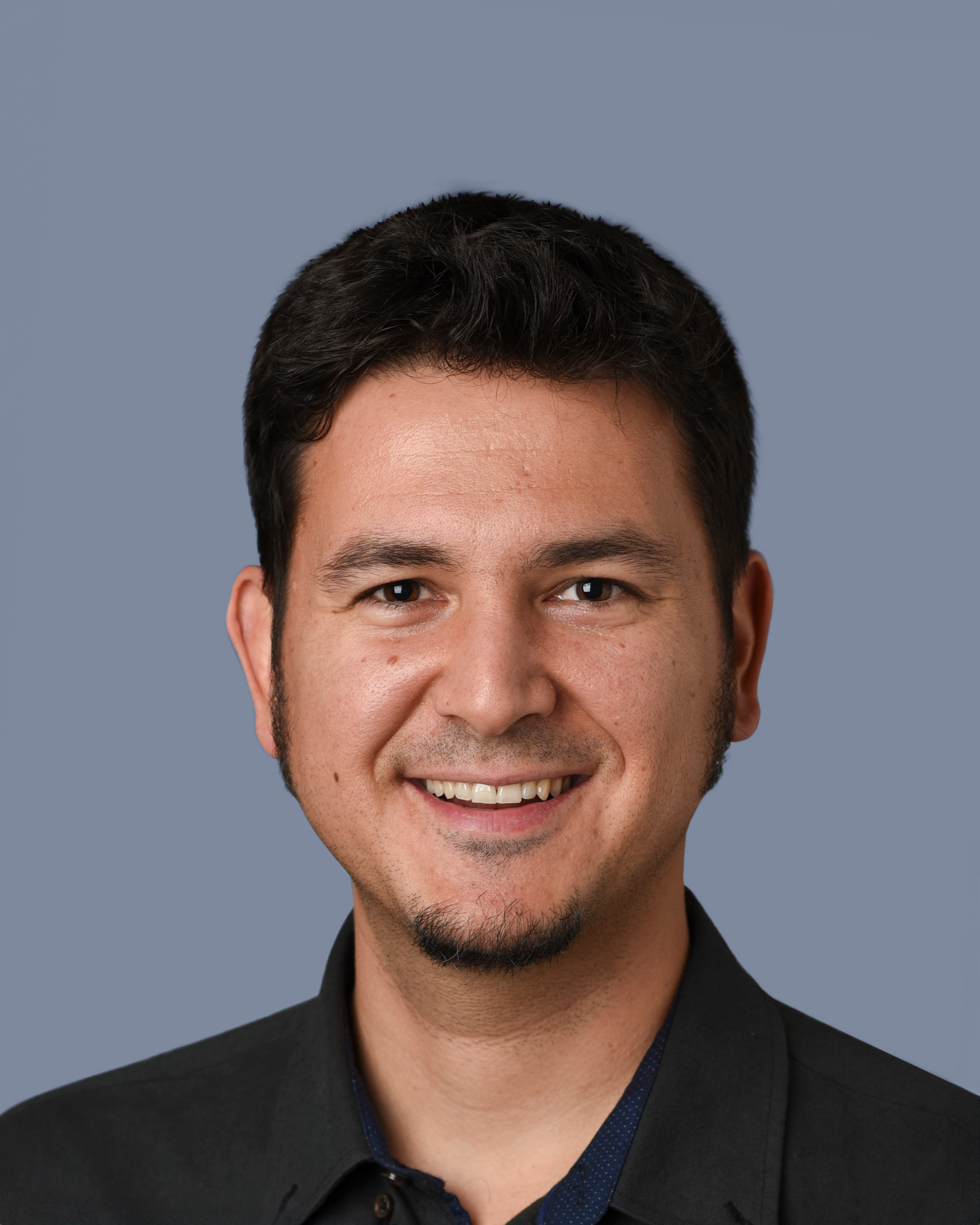
They will leverage instrumenting tools for data collection, deploy metrology for surface analysis, and create simulation models to achieve this.
The goal is to build a system allowing electronic design assessment, a faster and more robust way to succeed compared to multiple unsuccessful trials.
Along with that process, they will bring innovation to reinforce process control.
The complexity of the Abrasive Flow Machining behavior is a tremendous challenge. The media properties and the multiple parameters evolving along the process make it difficult to control the process. Creating models to predict the parameters and outcome adds to the challenge accurately.
Using a scientific methodology and leveraging numerical modeling software available at Penn State will significantly support the exploration, allowing for the validation of a robust simulation.
We can confirm that this is the spirit and that the PA Manufacturing Fellows Initiatives (PMFI) goals will be achieved.
We are also highly confident that this project supports Extrude Hone, a Pennsylvania manufacturer. It could help the company overcome the current limitations of the ORBITEX machinery and unlock the Orbital Abrasive Flow Machining potential.
Ultimately, this will reinforce Extrude Hone’s capabilities to penetrate new markets and contribute to the company’s prosperous future, enabling it to play its role in society, like contributing to local employment.
Meet Penn State and Extrude Hone’s experts at the April 5th Expo.
We thank Ph.D. student Hakan Toykoc, Professors Edward De Meter and Saurabh Basu for their work, and Penn State for this outstanding Manufacturing PA Innovation Program.
We are confident that many of you will visit the expo on April 5th at the Commonwealth Keystone Building in Harrisburg, PA.